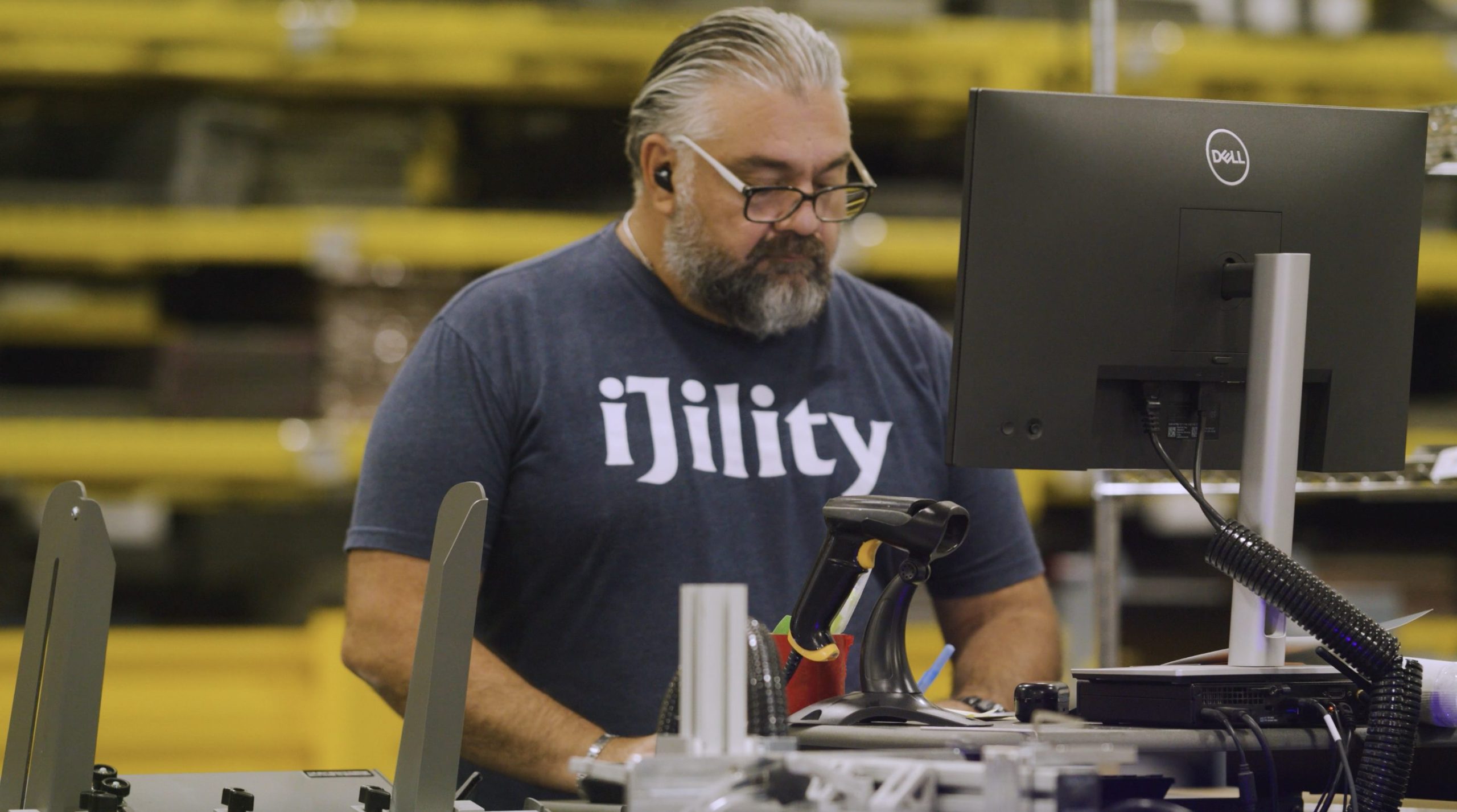
Even the most dedicated industry leaders can face unexpected setbacks that threaten productivity and profitability. One such manufacturer and distributor found themselves grappling with production backlogs, staffing issues, and frequent operational downtime. Despite their scale and experience, they struggled to maintain the service levels necessary to meet customer demand.
This case study explores how iJility, a leader in workforce and operations management, partnered with this manufacturer to turn things around. Through innovative solutions, advanced digital tools, and a strategic approach to workforce optimization, iJility helped their client eliminate inefficiencies, boost productivity, and achieve record output levels in just a few short weeks.
Identifying the Problem: A Production System Under Strain
For this international auto parts manufacturer, challenges were mounting across multiple areas of their operations. Production backlogs were affecting the entire facility, and despite running two weekday shifts producing 12,000 units per day, and one weekend shift producing 4,000 units, they struggled to keep up with demand.
There were several critical issues:
- Service Level Struggles: Meeting service level targets consistently proved difficult, prompting the company to even consider nearshoring as a solution.
- Operational Downtime: Significant periods of downtime due to work-cell setup and inconsistent maintenance schedules were further reducing productivity.
- Quality Control and Rework: Frequent quality issues required constant rework, adding to the delays.
- Staffing and Accountability: The company’s workforce was a mix of full-time employees and temporary labor. High absenteeism (42%) and a lack of accountability from staffing partners exacerbated the problem. Additionally, full-time employees were fatigued due to the rigorous overtime schedule, which averaged 20%.
Without a clear succession plan in place and facing mounting operational challenges, the company needed a solution that would not only resolve immediate issues but also create a foundation for long-term operational improvement.
iJility’s Approach: A Strategic Solution to Rebuild Efficiency
iJility began by conducting an in-depth discovery process, identifying the core issues hindering the manufacturer’s performance. It became clear that the company’s struggles were multifaceted, stemming from both workforce management and operational inefficiencies. iJility took a phased, strategic approach to address these challenges.
- High-Performance Teams for Labor Optimization
iJility deployed specialized teams of high-performing workers, starting with the weekend shift, which was experiencing the lowest output. These teams were carefully selected for their experience and ability to improve productivity under challenging circumstances. After successfully implementing these teams on weekends, iJility expanded the strategy to the weekday shifts, ensuring every operational hour was maximized for efficiency.
- Operational Alignment and Leadership Engagement
To maintain consistent alignment between iJility’s initiatives and the client’s goals, weekly operational meetings were established. These meetings involved key stakeholders from both iJility and the manufacturer, providing a platform for collaboration, problem-solving, and continuous improvement. This hands-on leadership engagement ensured that everyone was working towards the same objectives and allowed for quick adjustments when necessary.
- Leveraging Digital Tools for Continuous Improvement
One of iJility’s most impactful strategies was the introduction of digital tools that allowed for real-time tracking and data analysis. By implementing downtime tracking and a line changeover rate tracker, the manufacturer gained unprecedented visibility into their operations. This data not only provided immediate feedback for adjusting workflows but also enabled the company to continuously refine processes for optimal performance.
Process and Solutions: A Pathway to Sustainable Success
With a solid understanding of the manufacturer’s challenges, iJility set out to implement a series of solutions designed to not only resolve immediate pain points but also foster long-term operational efficiency.
- Weekend and Weekday Shift Optimization
A major hurdle for the manufacturer was the disparity in output between weekday and weekend shifts. Weekend shifts, in particular, were plagued by low productivity and higher operational costs due to inadequate staffing and reliance on overtime. iJility tackled this by assigning high-performance work teams to the weekend shift, which immediately increased output. After seeing marked improvements, iJility extended the same strategy to weekday operations, ensuring that both shifts were operating at peak capacity.
This shift restructuring was crucial in addressing production backlogs. By balancing labor more effectively and ensuring teams were well-prepared and fully staffed, the company saw a substantial increase in overall production. The enhanced organization and deployment of skilled workers across all shifts helped ensure that productivity remained consistent, regardless of the day of the week.
- Enhancing Quality Control and Reducing Rework
Quality control was another critical issue impacting the manufacturer’s efficiency. Frequent rework due to quality issues was not only time-consuming but also added to the operational costs. To address this, iJility overhauled the quality audit program, introducing more stringent tracking systems to catch issues earlier in the production process.
By implementing advanced tracking tools and introducing a site-wide dashboard, iJility provided real-time visibility into quality metrics. This enabled the client to quickly identify where issues were arising and address them before they snowballed into larger problems. The result was a drastic reduction in rework, leading to more efficient production and lower costs associated with defective products.
- Training and Cross-Training Programs for Workforce Flexibility
Recognizing the need for a more flexible and skilled workforce, iJility placed a strong emphasis on training and skill development. They refined training materials and processes to shorten the learning curve for new hires, ensuring that employees were quickly brought up to speed. In addition, cross-training programs were introduced, allowing workers to develop skills across multiple departments. This flexibility ensured that labor could be shared across different work cells, reducing bottlenecks and improving overall efficiency.
Cross-training not only improved operational fluidity but also boosted workforce morale, as employees felt more empowered and capable in their roles. This adaptability became a key factor in maintaining high productivity levels during peak periods, when the company needed all hands on deck to meet increased demand.
- Digital Tools for Operational Transparency and Improvement
iJility’s introduction of digital tools revolutionized how the manufacturer monitored and managed their operations. The implementation of a digital downtime tracking system allowed for precise data collection on equipment and process inefficiencies. This data was analyzed to pinpoint recurring issues, enabling the company to address them systematically rather than reactively.
Additionally, the line changeover rate tracker provided valuable insights into production transitions, an area that had been a significant source of delays. With these tools in place, the company could not only track and measure inefficiencies in real-time but also use the data to drive continuous improvement. This proactive approach to managing downtime and changeovers resulted in smoother transitions and less wasted time, further boosting production output.
The Results: Record-Breaking Output and Sustainable Efficiency
The results of iJility’s interventions were nothing short of remarkable. In just the first two weeks of implementation, the manufacturer saw a 100.5% increase in daily production volume, meeting and even exceeding their daily volume demands. The Units Per Hour (UPH) rate, a key measure of production efficiency, increased by 174.55%, with iJility’s teams achieving 178.18 UPH, far surpassing the department’s historical average of 153 UPH. This represented a 16.3% efficiency improvement.
The improvements didn’t stop there. By week three, iJility had helped the manufacturer clear the backlog that had been hampering their operations for months. With the backlog resolved, iJility then transitioned its workforce into five new work cells within the facility, ensuring that efficiency gains were spread across the entire production floor.
Thanks to cross-training and strategic workforce deployment, the manufacturer saw week-over-week improvements in efficiency across all shifts. The decision was made to have iJility fully manage the weekend shift, a testament to the trust and confidence the manufacturer had in iJility’s methods.
By the end of the 12-week engagement, iJility had not only met the initial goals of increasing production and reducing backlogs but had also helped the manufacturer achieve record output levels while reducing operational costs associated with rework, absenteeism, and inefficiency.
Conclusion: Transforming Challenges into Opportunities with iJility’s Expertise
This case study highlights how iJility’s data-driven approach, combined with their expertise in workforce management and operational efficiency, enabled an auto parts manufacturer to overcome significant challenges and achieve sustainable success. Through strategic initiatives, advanced digital tools, and a focus on training and performance, iJility turned a struggling operation into a high-performing, efficient machine.
For companies facing similar challenges, the iJility methodology offers a clear path to not only resolving current issues but also building a foundation for long-term growth and efficiency. By leveraging the right people, processes, and technology, iJility can help transform any operation into a model of productivity and success.
About iJility
iJility is a leading provider of workforce optimization solutions, specializing in supply chain operations and on-site management. With a focus on reducing turnover and increasing productivity, iJility delivers customized strategies that align with client-specific goals. Their experienced leadership team integrates data-driven decision-making and innovative solutions to address today’s competitive labor market challenges. Businesses gain access to scalable, dependable workforce solutions designed to optimize operational efficiency and drive measurable results when they partner with iJility. Schedule a discovery call with iJility today.
Author: iJility