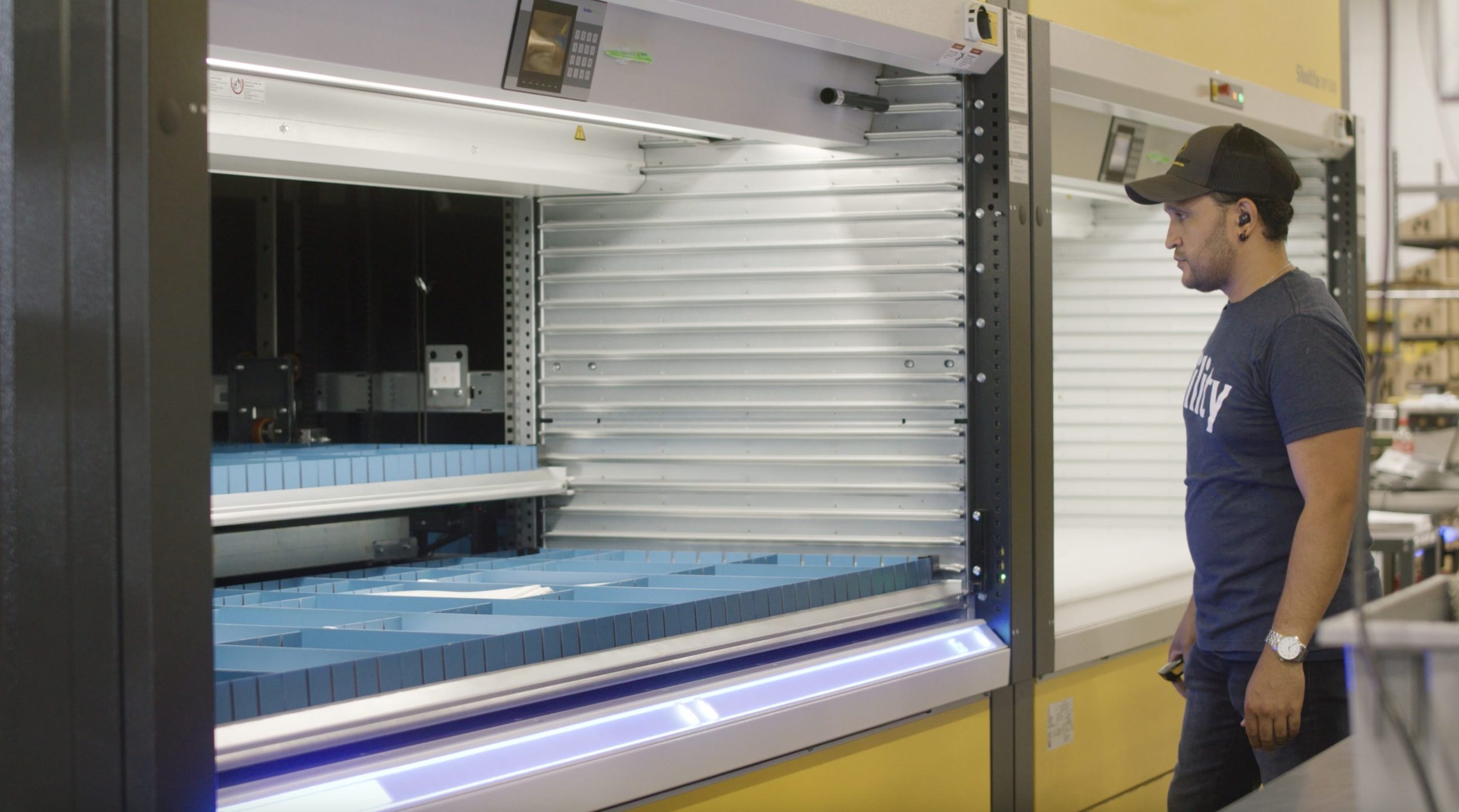
For many operations managers in the manufacturing environment, the pressure to maintain high-quality standards while managing costs can feel like walking a tightrope. As an operations manager, you know that quality cannot be compromised, yet increasing headcount to achieve this isn’t always a feasible option. Fortunately, there are several strategies you can implement to ensure quality without adding more personnel. These tactics focus on streamlining processes, optimizing current resources, and leveraging technology to enhance efficiency.
Here are five actionable tips to maintain and even improve product quality while keeping your headcount steady.
Standardize Workflows and Procedures
One of the most effective ways to maintain consistency and quality in manufacturing is by standardizing workflows. Variability in processes leads to errors, inefficiencies, and inconsistent product quality, but standardized procedures create a foundation that every worker can rely on.
How to Implement:
- Document Every Step: Create clear, detailed documentation for every process, from machine operation to quality control checks. Ensure that these are easily accessible to your team.
- Training and Reinforcement: Equip your staff with thorough training and periodically refresh their knowledge with ongoing education. This reduces the chances of process deviations and helps everyone stay on the same page.
- Use Visual Aids: Charts, diagrams, and step-by-step instructions can be posted on the shop floor to provide workers with quick reminders.
Benefit: Standardized processes minimize variability and reduce the need for constant supervision or rework, enhancing quality without needing extra staff.
Invest in Automation and Smart Technology
Automation is not about replacing jobs—it’s about optimizing your current workforce and reducing human error. With advancements in smart manufacturing technologies like IoT (Internet of Things) devices and machine learning, you can now monitor and improve quality in real time without expanding your team.
How to Implement:
- Deploy Sensors for Monitoring: Integrate IoT sensors to monitor equipment performance and product quality throughout the production process. This real-time data helps identify issues before they become problems.
- Automated Quality Control (QC): Use automated inspection systems like vision technology to ensure that every product meets your standards without the need for manual checks.
- Predictive Maintenance: Implement predictive maintenance to monitor machinery health and avoid downtime. Keeping machines in optimal condition prevents quality defects due to equipment malfunctions.
Benefit: Automation allows your existing staff to focus on high-value tasks while the technology handles repetitive quality checks and data monitoring, ensuring consistent output without needing additional workers.
Implement Lean Manufacturing Principles
Lean manufacturing is a proven strategy to enhance productivity while minimizing waste. When applied effectively, it can lead to higher quality output by ensuring that every step in the production process adds value.
How to Implement:
- Identify and Eliminate Waste: Evaluate your processes for any form of waste—whether it’s excess material usage, time inefficiencies, or unnecessary motions on the shop floor.
- Continuous Improvement (Kaizen): Encourage a culture of continuous improvement, where every team member is empowered to identify issues and suggest process improvements.
- Just-in-Time Production (JIT): Reduce inventory waste by adopting JIT production, which ensures that materials and components are delivered exactly when they are needed, reducing the likelihood of defects from excess handling or storage.
Benefit: Lean principles maximize your existing resources, allowing you to maintain or improve quality without requiring additional staff to handle inefficiencies or quality lapses.
Strengthen Supplier Relationships
High-quality raw materials and components are crucial to producing high-quality products. Ensuring that your suppliers maintain stringent quality standards can significantly reduce the amount of rework and quality control needed on your end.
How to Implement:
- Develop Clear Quality Requirements: Work closely with suppliers to ensure they understand and meet your quality expectations. This can include specifying tolerances, certifications, or testing procedures.
- Collaborative Improvement: Establish a partnership where you can work together with your suppliers to continuously improve material quality. This could involve joint audits or providing feedback on their processes.
- Supplier Audits: Conduct regular audits or quality checks on incoming materials to ensure that they meet your standards. Catching issues early prevents defects from slipping into your production line.
Benefit: By fostering strong supplier relationships and ensuring they deliver quality materials, you reduce the need for corrective actions downstream, allowing your team to stay focused without expanding headcount.
Enhance Cross-Departmental Collaboration
Quality isn’t just the responsibility of the production team; it’s a company-wide goal. Promoting better communication and collaboration across departments—like design, engineering, procurement, and logistics—helps catch potential quality issues before they reach the production floor.
How to Implement:
- Cross-Functional Teams: Form cross-functional teams that include members from different departments to work on product development and process improvement. Diverse perspectives lead to more comprehensive problem-solving.
- Integrated Software Solutions: Use collaborative software platforms to ensure all departments have access to real-time data, minimizing the risk of miscommunication or siloed information.
- Feedback Loops: Establish feedback loops between production and design/engineering teams to ensure that design flaws or process inefficiencies are quickly addressed and corrected.
Benefit: By improving collaboration, you can prevent quality issues from arising due to poor communication or misaligned goals between departments, all while using your current workforce more effectively.
The Final Takeaway
Ensuring high quality in manufacturing doesn’t always mean adding more people to the team. By optimizing processes, leveraging technology, and improving collaboration, you can achieve your quality goals efficiently. Standardizing workflows, embracing automation, adopting lean principles, collaborating with suppliers, and fostering cross-department communication are all strategies that empower your existing workforce to do more, without compromising on quality.
As an operations manager, your ability to drive efficiency and maintain quality will not only save costs but also give your company a competitive edge—without the need to increase headcount.
At iJility, we are committed to helping businesses like yours optimize their workforce and overcome labor challenges. Schedule a discovery call to learn how we can help you build a custom solution with fast results.
Author: iJility