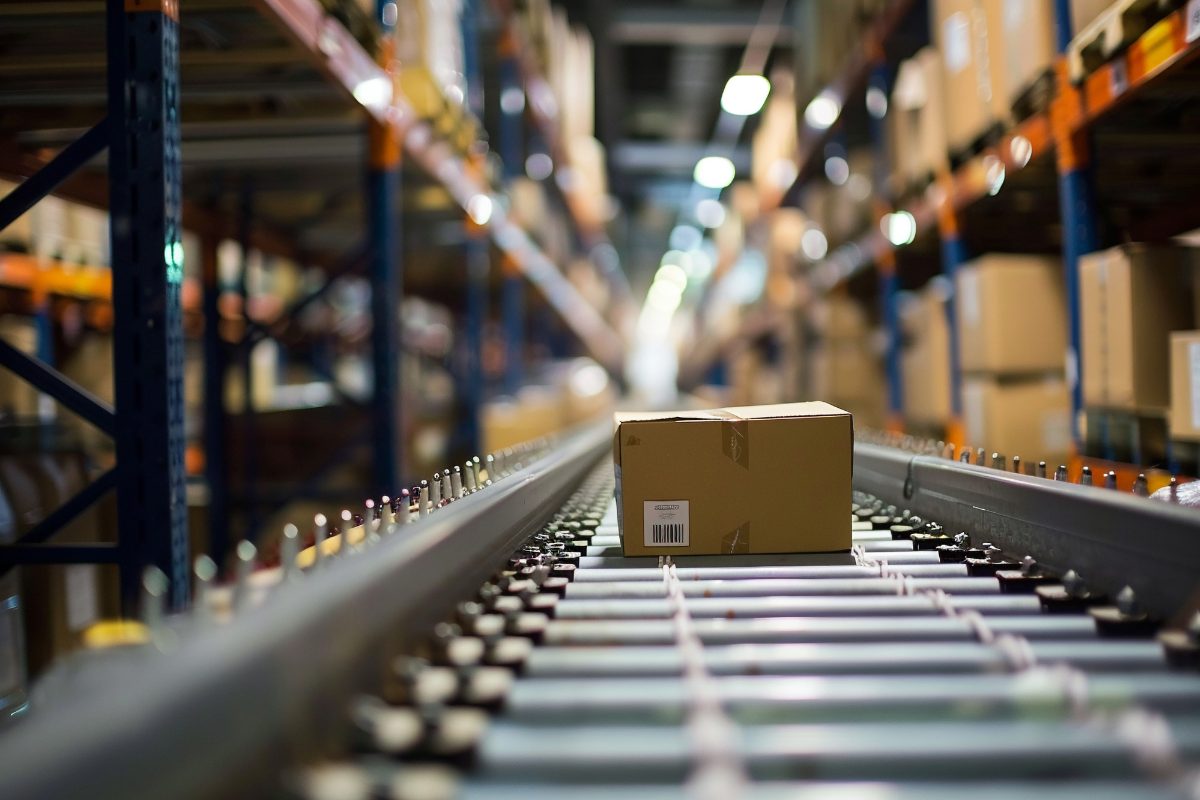
Operational inefficiencies can be costly in supply chain, logistics, distribution, e-commerce, and manufacturing environments. However, identifying the exact problems isn’t always straightforward. If you’re unsure where bottlenecks or inefficiencies exist, there are key indicators that can help you diagnose potential issues before they become critical.
Warning Signs of Workflow Inefficiencies
- Frequent Bottlenecks and Slowdowns
If you notice frequent delays at certain points in your operation—whether it’s order fulfillment, assembly lines, or shipping—there’s likely a process inefficiency. Common causes include:
- Understaffing or improperly allocated labor
- Equipment failures or outdated technology
- Ineffective inventory management
- High Labor Costs Without Productivity Gains
Are labor costs rising while output remains stagnant? This could indicate:
- Over-reliance on manual tasks instead of automation
- Poor training and onboarding processes
- Lack of cross-training, causing inefficiencies when employees are absent
- Excessive Overtime or Overworked Employees
Consistently high overtime expenses or employee burnout can be red flags. These issues might stem from:
- Poor workload distribution
- Staffing shortages
- Fluctuations in demand not accounted for in workforce planning
- Quality Control Issues
A spike in defects, returns, or complaints suggests operational shortcomings. Quality issues often arise due to:
- Inconsistent training
- Poor process standardization
- Rushed production due to workforce shortages
- Low Employee Engagement and High Turnover
Unhappy employees are less productive and more likely to leave, increasing recruitment and training costs. Signs of engagement problems include:
- High absenteeism
- Low morale
- Increased conflict or miscommunication
- Inventory Discrepancies
Miscalculations in stock levels, frequent stockouts, or excessive surplus inventory can signal:
- Inefficient inventory tracking systems
- Poor demand forecasting
- Warehouse layout inefficiencies
- Inconsistent Order Fulfillment Times
If order processing times are unpredictable, you may need to assess:
- Picking and packing workflows
- Technology integration across supply chain stages
- Labor force consistency and efficiency
How to Address These Issues Without a Clear Diagnosis
Even if you can’t pinpoint the exact source of inefficiencies, there are proactive steps you can take to streamline your operations.
- Implement Real-Time Data Tracking
Data provides insight into inefficiencies. Using workforce analytics, production tracking, and inventory management tools can help detect patterns in delays and bottlenecks.
- Cross-Train Employees
Developing a flexible workforce allows employees to step into multiple roles, reducing workflow disruptions when someone is absent and improving overall efficiency.
- Adopt Lean Principles
Lean methodologies help eliminate waste, whether it’s unnecessary movement, redundant processes, or excessive inventory.
- Evaluate Technology and Automation
Assess whether outdated systems or manual tasks are slowing operations. Upgrading warehouse management systems (WMS), using robotics, or integrating AI-driven forecasting tools can significantly improve efficiency.
- Optimize Workforce Planning
Matching staffing levels to operational demand ensures resources are used efficiently. This includes:
- Seasonal workforce adjustments
- Reducing dependency on temporary labor
- Aligning training programs with operational needs
- Conduct Regular Process Audits
Routine evaluations of workflows help catch inefficiencies before they escalate. This can include:
- Time studies on key tasks
- Employee feedback surveys
- Performance benchmarking
How iJility Can Help
At iJility, we understand that operational challenges don’t always have an obvious cause. That’s why we provide tailored workforce solutions designed to address inefficiencies in your supply chain, distribution, and manufacturing operations.
Our services include:
- Customized workforce planning to optimize staffing levels and minimize costs
- Process improvement strategies that enhance efficiency and productivity
- Technology integration to streamline workflow and improve tracking
- Training and workforce development to boost employee engagement and performance
Discover the Benefits of an iJilitySTUDY
If you’re unsure where your operational inefficiencies lie, our iJilitySTUDY™ can help. This in-depth analysis assesses your current workflows, identifies hidden inefficiencies, and provides actionable recommendations tailored to your unique needs.
With iJility’s expertise, you can improve productivity, reduce costs, and enhance operational agility without wasting resources on trial-and-error solutions.
Let’s optimize your workflow together. Schedule a discovery call with iJility today.
Author: Carl Scott