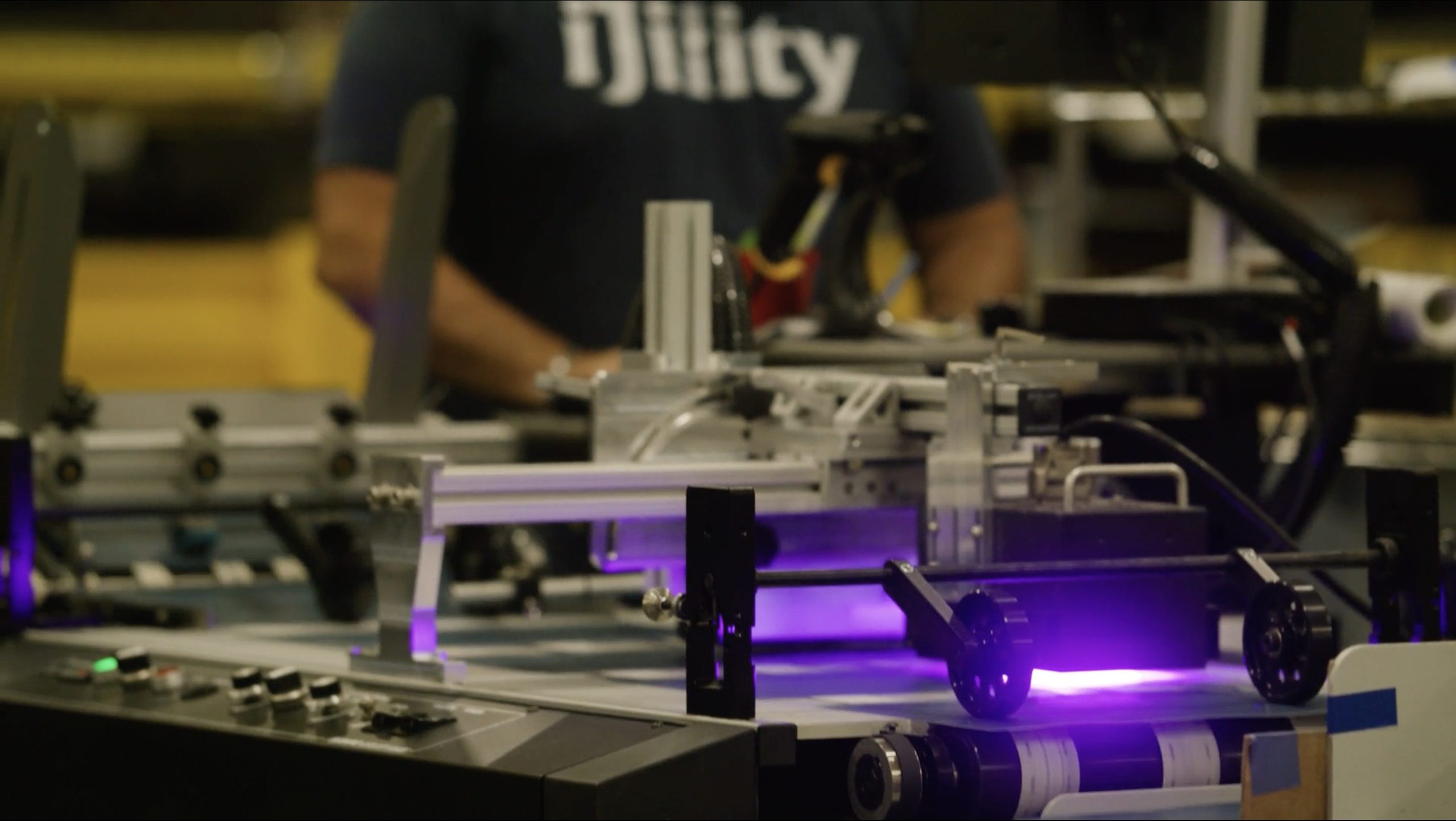
In today’s competitive industries—whether it’s manufacturing, logistics, or e-commerce—staying ahead requires more than advanced technology or streamlined processes. It demands a workforce that is engaged, proactive, and committed to continuous improvement. Creating a culture where employees feel empowered to innovate, problem-solve, and enhance their skills isn’t just a nice-to-have—it’s a strategic imperative.
But what does a culture of continuous improvement really mean, how can it be implemented effectively, and what benefits can businesses expect? Let’s break it down.
What Is a Culture of Continuous Improvement?
Continuous improvement is a mindset of consistently seeking ways to improve processes, products, and services. It’s about fostering an environment where employees aren’t just following instructions but are actively engaged in identifying inefficiencies, testing solutions, and optimizing their work.
Unlike one-off improvement projects or temporary initiatives, a culture of continuous improvement embeds this mindset into the DNA of the organization. It’s not limited to leadership or operational managers—every employee, from warehouse workers to drivers, becomes a contributor.
How to Implement Continuous Improvement in the Workplace
Building this culture isn’t about overnight transformation. It’s a gradual, intentional process that requires commitment, tools, and the right mindset. Here’s how to start:
- Empower Your Workforce
Employees on the front lines—whether they’re in the warehouse or managing transportation logistics—are uniquely positioned to identify inefficiencies. Give them a voice. Regularly solicit feedback through team meetings, suggestion boxes, or digital platforms. When employees know their input matters, they’re more likely to engage in problem-solving.
Tips to Empower:
- Recognize contributions publicly, no matter how small.
- Provide decision-making authority for operational adjustments within their roles.
- Establish open-door policies with supervisors and managers.
- Provide Training and Development Opportunities
Continuous improvement relies on continuous learning. Invest in training programs that enhance both technical and soft skills. From Lean Six Sigma principles to advanced software training for logistics, these tools can help employees become more effective in their roles and inspire innovation.
Training Ideas:
- Host workshops on operational efficiency techniques.
- Create mentorship programs pairing experienced employees with newer hires.
- Use gamified e-learning platforms to make skill development engaging.
- Adopt the Right Metrics and Tools
Without measurable goals, it’s impossible to gauge improvement. Use data to track performance, identify trends, and benchmark progress. From inventory management software to KPI dashboards for transportation efficiency, leveraging technology is key.
Actionable Steps:
- Define KPIs that align with your business goals (e.g., order fulfillment time, error rates, transportation costs).
- Regularly review these metrics with employees to showcase their impact.
- Offer tools like handheld scanners, route optimization software, or inventory trackers that simplify tasks and improve accuracy.
- Create a Safe Space for Experimentation
True improvement requires a willingness to test new ideas—and sometimes fail. Employees won’t take risks if they fear blame. By creating a psychologically safe environment, you enable your team to innovate without fear of repercussions.
How to Foster Safe Experimentation:
- Encourage pilot projects for new ideas on a small scale.
- Celebrate lessons learned from failures as much as successes.
- Use failures as opportunities to refine and improve processes.
- Celebrate Wins—Big and Small
Improvement takes effort, and recognition is a powerful motivator. Celebrate milestones, whether it’s an individual’s idea reducing cycle time or a team effort that slashes transportation delays. Recognition fuels morale and reinforces the value of improvement.
Recognition Practices:
- Share success stories in company newsletters or meetings.
- Offer small incentives like gift cards, lunch outings, or time off.
- Host an annual awards ceremony recognizing continuous improvement champions.
The Benefits of a Continuous Improvement Culture
Why invest the time, energy, and resources into fostering this culture? The rewards are far-reaching and impactful.
- Enhanced Efficiency and Cost Savings
A workforce that constantly looks for ways to optimize processes can lead to significant cost reductions. Whether it’s trimming waste in reverse logistics or improving order accuracy in e-commerce, small, continuous changes add up.
- Higher Employee Engagement and Retention
When employees feel their contributions matter and they’re part of a larger purpose, engagement soars. This translates into lower turnover rates—critical for industries like manufacturing and logistics, where skilled labor shortages are common.
- Greater Innovation
Continuous improvement encourages out-of-the-box thinking. Over time, this leads to innovative solutions that give businesses a competitive edge, such as improved packaging techniques or streamlined kitting processes.
- Improved Customer Satisfaction
Efficiency and innovation lead to better service delivery. Happier customers mean repeat business, stronger partnerships, and a stellar reputation in your industry.
Final Thoughts
Creating a culture of continuous improvement isn’t just a lofty goal—it’s a practical strategy for staying competitive in fast-paced industries. By empowering employees, offering training, embracing metrics, and celebrating achievements, you can cultivate a workforce that’s not only more productive but also more engaged and innovative.
At the heart of this culture is the recognition that improvement isn’t about perfection; it’s about progress. When employees see themselves as active participants in shaping the success of your business, the results can be transformative—for your workforce, your operations, and your bottom line.
Let’s work together to build a workplace where improvement isn’t just an initiative—it’s a way of life.
About iJility
iJility is committed to helping businesses optimize operations by connecting them with the right talent and fostering a culture of excellence.
Ready to unlock the full potential of your workforce? Schedule a discovery call with us today to learn how iJility can help you achieve your operational goals.
Author: iJility