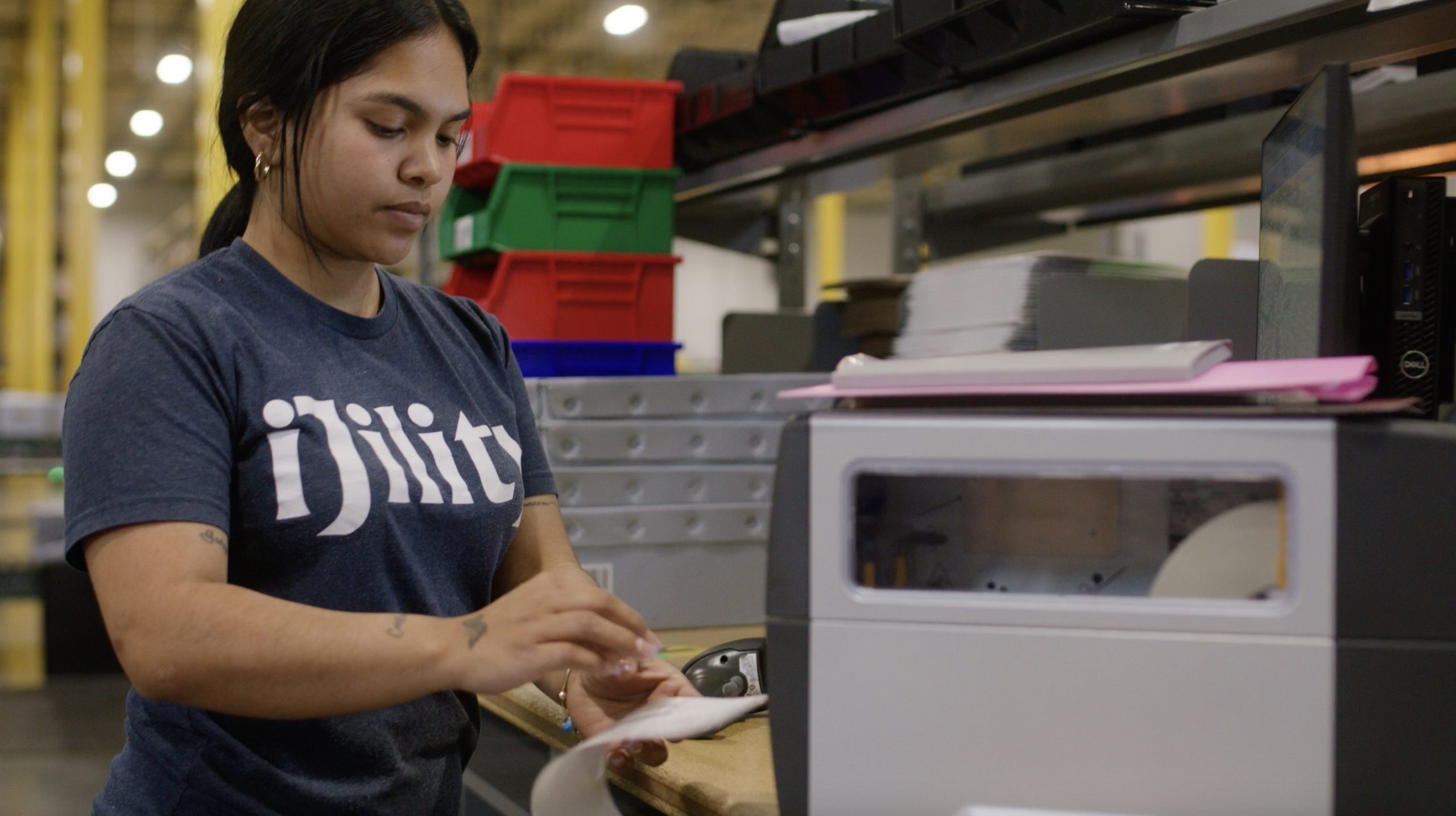
The pressure to meet high production demands is constant in industries like manufacturing, logistics, and supply chain management. Businesses often face a critical question: should they prioritize quality or quantity? The truth is that long-term success depends on finding the right balance between the two.
Achieving this equilibrium isn’t just about advanced tools or streamlined processes—it’s about having a well-trained, cross-trained, and flexible workforce. Let’s explore why a strong workforce is critical to balancing quality and quantity, how cross-training boosts efficiency and productivity, and actionable tips for implementing these strategies in your operations.
The Quality vs. Quantity Dilemma
Every operation grapples with the challenge of producing at scale without compromising on quality. Prioritizing quantity might get more units out the door, but it risks customer dissatisfaction and costly returns if quality suffers. On the other hand, hyper-focusing on quality at the expense of speed can lead to missed deadlines and higher labor costs.
Striking the right balance means scaling output efficiently while maintaining consistent quality—and that’s where your workforce plays a pivotal role.
The Role of a Well-Trained Workforce
Your workforce is at the heart of balancing quality and quantity. A well-trained, engaged team doesn’t just execute tasks; they anticipate problems, maintain standards, and adapt to changes without losing productivity.
Why Training Matters
- Consistency: Properly trained employees are less likely to make mistakes, ensuring uniform product quality.
- Speed: Skilled workers can complete tasks faster without sacrificing accuracy.
- Problem-Solving: Trained employees can identify inefficiencies and suggest improvements, streamlining processes.
Cross-Training: The Key to Flexibility
Cross-training—teaching employees to perform multiple roles—adds another layer of efficiency and resilience to your operations. Here’s why it’s essential:
- Fills Skill Gaps
When employees can step into different roles as needed, you reduce downtime caused by absenteeism or turnover.
- Improves Workflow Efficiency
Cross-trained employees understand how their tasks impact the entire process, leading to better collaboration and fewer bottlenecks.
- Boosts Employee Engagement
Learning new skills keeps employees engaged and motivated, which translates into higher productivity and lower turnover rates.
Balancing Quality and Quantity Through Workforce Strategies
To achieve the perfect balance, businesses need to invest in their workforce strategically. Here are actionable steps to get started:
- Develop a Comprehensive Training Program
Training should go beyond onboarding. Regular, ongoing skill development ensures employees are equipped to meet evolving demands.
Steps to Take:
- Create clear standard operating procedures (SOPs) for every task.
- Offer regular refresher courses to reinforce best practices.
- Use technology like e-learning platforms to provide scalable training options.
- Implement Cross-Training Programs
Cross-training shouldn’t be an afterthought. Make it a core part of your workforce strategy.
How to Implement:
- Rotate employees through different roles on a regular schedule.
- Pair less experienced workers with mentors for hands-on learning.
- Track employees’ competencies to identify gaps and opportunities for cross-training.
- Leverage Data for Workforce Optimization
Data can provide valuable insights into where your workforce excels and where improvements are needed.
Use Metrics Like:
- Error rates to identify training gaps affecting quality.
- Cycle times to pinpoint inefficiencies in production speed.
- Employee performance data to identify candidates for advanced training.
- Foster a Culture of Accountability
When employees take ownership of both quality and quantity, the results are transformative.
Tips for Building Accountability:
- Set clear, measurable goals for quality and productivity.
- Regularly share performance feedback with employees.
- Celebrate successes and recognize contributions that enhance both quality and quantity.
The Efficiency and Productivity Connection
A strong, flexible workforce doesn’t just balance quality and quantity—it drives overall efficiency and productivity. Here’s how:
- Fewer Errors = Less Waste
A trained workforce reduces mistakes, minimizing wasted materials and rework.
- Streamlined Processes = Faster Output
Cross-trained employees eliminate bottlenecks, keeping workflows smooth.
- Employee Engagement = Higher Output
Engaged employees are more productive, ensuring both quality and speed are met.
Why It Matters for Long-Term Success
In industries like supply chain logistics or manufacturing, balancing quality and quantity isn’t just an operational goal—it’s a competitive advantage. Customers expect consistent, high-quality products delivered on time, and businesses that meet these expectations earn loyalty and repeat business.
The key to achieving this lies not just in technology or processes but in empowering your workforce. When your employees are skilled, adaptable, and motivated, they become the driving force behind your ability to scale output without compromising quality.
The Takeaway
Striking the right balance between quality and quantity is no easy task, but it’s achievable with the right workforce strategies. Investing in a well-trained, cross-trained, and engaged team ensures you can meet production goals efficiently while maintaining high standards.
At iJility, we understand the critical role a flexible workforce plays in operational success. We connect businesses with skilled, adaptable talent to enhance efficiency, productivity, and quality.
Schedule a discovery call today to learn how iJility can help you achieve the perfect balance in your operations!
Author: iJility