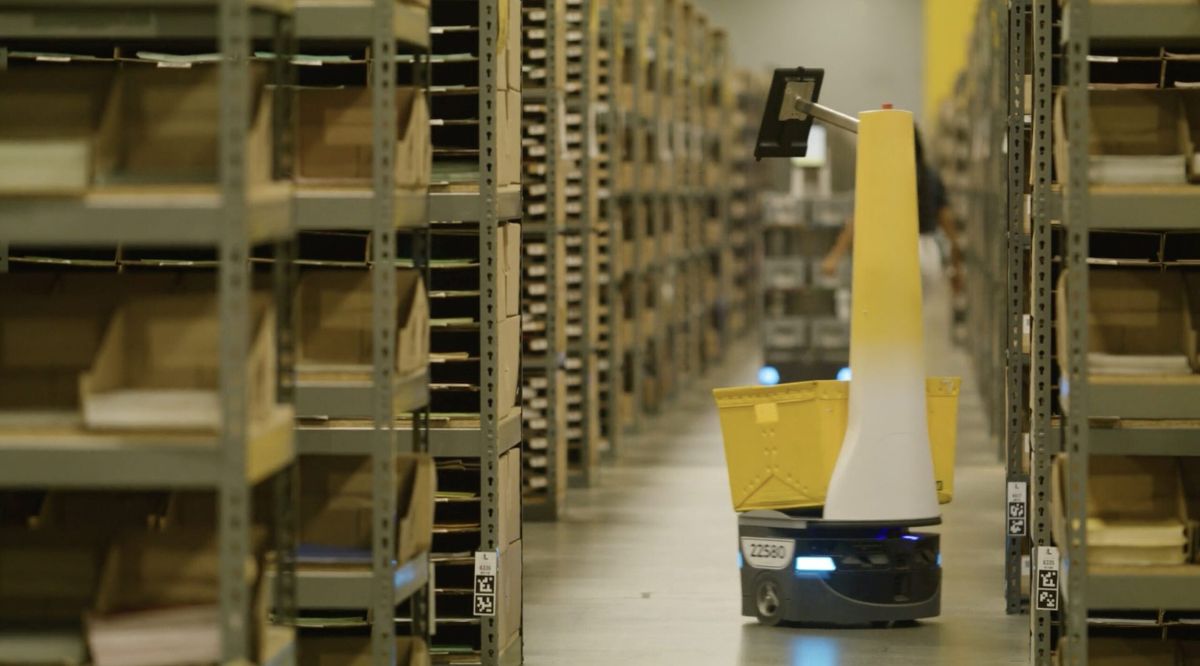
In the fast-paced world of manufacturing, logistics, and supply chain management, efficiency is everything. Businesses are under constant pressure to deliver faster, reduce errors, and keep costs in check—all while managing a tight labor market. Enter automation: a game-changing solution that’s transforming how operations managers approach direct labor costs.
Automation can reduce labor expenses without sacrificing quality or morale. Two big questions are: what types of automation are most effective, and how do operations strike the right balance between people and machines?
The Labor Cost Challenge
Direct labor costs often represent one of the largest expenses in industries like logistics, transportation, and manufacturing. Rising wages, employee turnover, and inefficiencies compound the problem, cutting into already thin margins. Traditional cost-saving methods—like headcount reduction—can often lead to lower morale and higher error rates, making them unsustainable.
Automation, when implemented strategically, offers a better way forward.
How Automation Reduces Labor Costs
Automation doesn’t replace workers; it enhances their productivity and minimizes waste. Here’s how automation directly addresses labor cost challenges:
- Increased Productivity
Automated systems can operate continuously, without breaks or fatigue. Tasks that might take hours for manual workers can be completed in minutes, allowing your team to focus on higher-value activities.
Example:
Automated picking systems in warehouses can retrieve items faster and with greater accuracy than manual pickers, reducing the time and labor needed for order fulfillment.
- Lower Error Rates
Human error can lead to costly mistakes, from mis-shipments in e-commerce to assembly line defects in manufacturing. Automation minimizes these risks by standardizing repetitive tasks.
Example:
Barcode scanning systems in reverse logistics ensure returns are processed correctly, avoiding the costs of reprocessing or customer dissatisfaction.
- Flexibility for Variable Demand
In industries with seasonal or fluctuating demand, automation provides scalability. Robots and software systems can ramp up or down based on workload, reducing the need to hire and train temporary workers.
Example:
Automated packaging systems adjust to handle increased volume during peak seasons like the holidays without requiring extra staffing.
- Reduced Onboarding and Training Costs
Bringing new hires up to speed takes time and resources. Automation eliminates the need for extensive onboarding in certain roles, allowing businesses to allocate training budgets elsewhere.
Example:
Self-driving forklifts in warehouses can perform tasks without requiring operators to undergo certification or training.
Types of Automation Making an Impact
Not all automation is created equal. Here are the technologies making waves in reducing direct labor costs:
- Robotic Process Automation (RPA)
RPA handles repetitive, rule-based tasks like data entry, inventory updates, and invoice processing, freeing up administrative staff to focus on strategic work.
- Collaborative Robots (Cobots)
Cobots work alongside human employees, enhancing productivity without fully replacing the workforce. They’re ideal for tasks like assembly, sorting, or palletizing.
- Automated Guided Vehicles (AGVs)
AGVs are transforming transportation within facilities. They efficiently move materials between workstations, reducing the need for manual labor in warehouse and manufacturing environments.
- AI and Machine Learning
AI-driven analytics predict demand, optimize schedules, and streamline workflows, ensuring that your workforce is deployed as efficiently as possible.
- Automated Packaging Systems
From shrink wrapping to customized boxing, these systems reduce manual intervention in the final stages of the supply chain, cutting labor costs while boosting accuracy.
Balancing Automation with a Human Workforce
While automation delivers undeniable cost savings, it’s essential to strike a balance between machines and human employees. Over-automation can lead to workforce resistance, skill gaps, and loss of institutional knowledge. Here’s how to maintain equilibrium:
- Engage Employees Early
Involve your workforce in automation initiatives. When employees understand that automation is there to assist rather than replace them, they’re more likely to embrace it.
- Upskill Your Team
Offer training to help employees adapt to new roles created by automation, such as operating advanced machinery or analyzing data from AI systems.
- Preserve Human-Centered Roles
Not all tasks should be automated. Customer service, creative problem-solving, and leadership roles require the human touch and remain critical to operational success.
The Benefits of Automation
When implemented thoughtfully, automation delivers far-reaching advantages beyond labor cost savings:
- Improved Consistency: Automation ensures uniformity in processes, boosting quality and customer satisfaction.
- Scalability: Businesses can grow without being limited by labor constraints.
- Enhanced Safety: Automation reduces workplace injuries by taking on hazardous or physically demanding tasks.
- Sustainability: Streamlined processes can lower energy use and waste, aligning with environmental goals.
The Final Takeaway
Automation is reshaping how supply chain, manufacturing, and related industries operate, offering a smarter way to manage direct labor costs. It’s not about replacing people—it’s about empowering them to do more, better. With the right technologies and a commitment to balance, businesses can create a future where humans and machines work together seamlessly.
Ready to explore how automation can transform your workforce strategy? iJility is here to help.
About iJility
iJility specializes in workforce solutions for supply chain logistics, reverse logistics, manufacturing, and more. Our expertise in connecting businesses with talent and technology ensures you stay ahead in an ever-changing landscape.
Let’s discuss how automation can enhance your operations and reduce labor costs. Schedule a discovery call today to take the first step!
Author: iJility