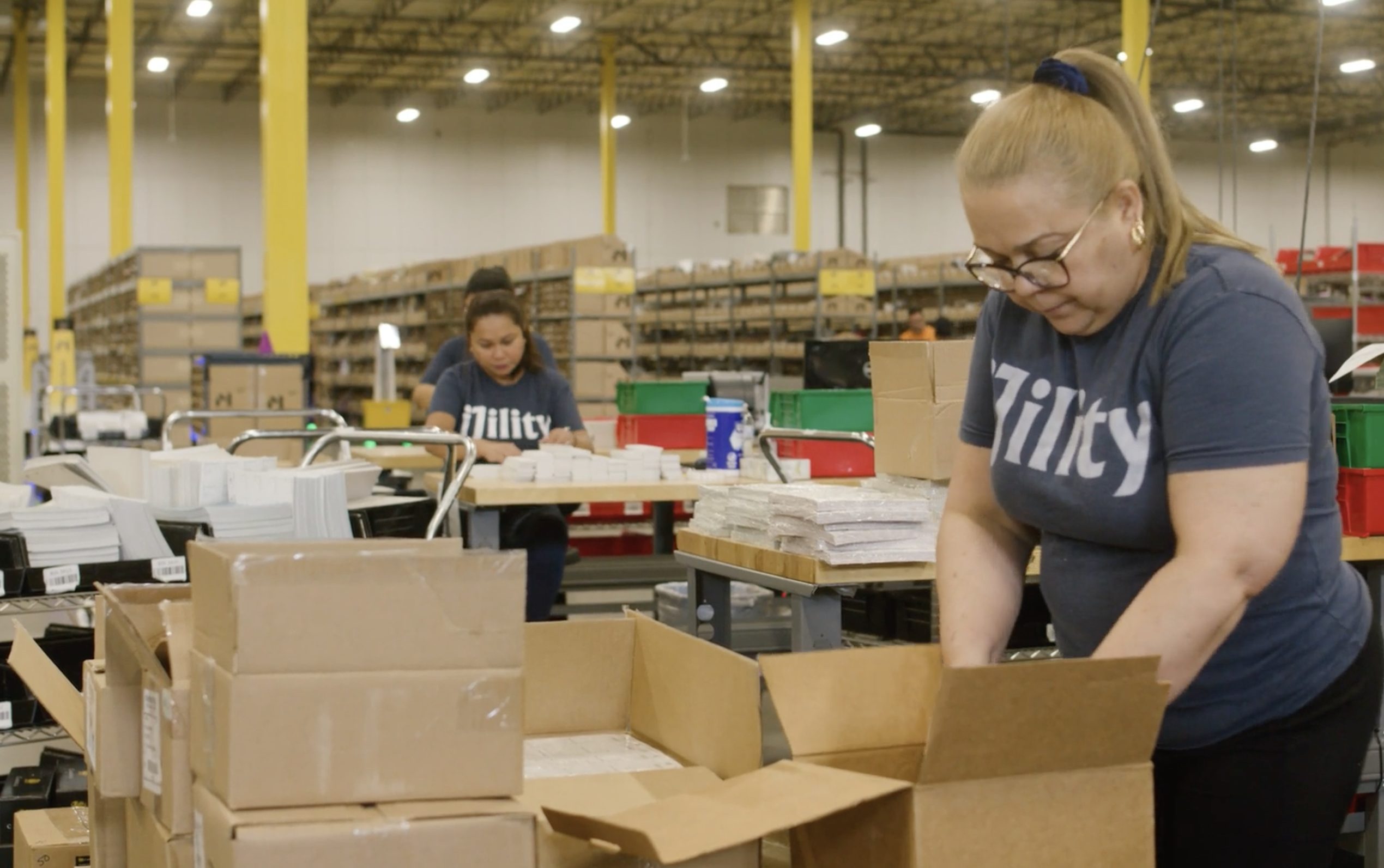
There’s no doubt that port disruptions have become an almost inevitable challenge. Labor strikes, natural disasters, political instability, and equipment malfunctions can all lead to port delays, creating a domino effect throughout the supply chain. For managers in operations, logistics, or shipping, these disruptions can translate into increased costs, missed deadlines, and strained customer relationships. To minimize the impact, a proactive approach from a workforce perspective is essential, particularly by embracing innovative staffing models like the Cost Per Unit (CPU) model. Unlike traditional hourly pricing, CPU offers a more flexible, cost-effective solution that helps companies adapt to these fluctuations while maintaining efficiency.
Challenges of Port Disruptions
Port disruptions can arise from a variety of causes, each bringing unique complications. Let’s take a look at some of the primary challenges and how they impact both operations and the workforce:
- Labor Strikes: Labor strikes are often prompted by wage disputes, unsafe working conditions, or contractual disagreements. When dockworkers or other port employees strike, the entire port can come to a standstill, causing extensive delays. The ripple effect can increase labor costs as workforce teams may require overtime to keep pace with delayed shipments.
- Natural Disasters: Ports are vulnerable to natural disasters like earthquakes, hurricanes, and floods, which can render them temporarily or permanently unusable. These situations create immense stress on the workforce, as they’re often tasked with rerouting shipments or expediting delivery times to mitigate the disruption’s impact on customers.
- Political Instability: Political unrest can result in port closures or restricted access to key trade routes. In politically unstable regions, workers may be asked to prioritize alternative routes, increase security measures, or quickly adapt to sudden closures. The unpredictability of these events can strain resources and demand quick workforce redeployment.
- Equipment Malfunctions: Modern ports depend on complex machinery like cranes, loading docks, and automated systems. Any malfunction can slow down port operations, causing a backlog that requires workforce teams to adjust schedules, work overtime, or shift to manual labor solutions. These disruptions add operational costs, especially if they require hiring temporary labor or paying premium rates for after-hours work.
Ramifications of Port Disruptions for the Customer
The consequences of port disruptions don’t just impact logistics companies; they also have significant downstream effects for customers. Key impacts include:
- Delays in Deliveries: A delay at the port means goods reach customers later than expected, which can strain customer relationships and even lead to lost sales.
- Increased Costs: Shipping delays often mean higher costs, from expedited freight charges to storage fees. When these are passed on to customers, it can reduce competitiveness.
- Inconsistent Supply: Disruptions may lead to inconsistent product availability, complicating inventory management for businesses that rely on just-in-time (JIT) supply chain models.
- Reduced Customer Trust: When delays become frequent, customers may seek more reliable suppliers, impacting long-term loyalty.
These challenges underline the need for operational flexibility. Workforce management plays a critical role in responding quickly to these challenges, particularly when optimized through the CPU model.
Strategies for Handling Disruptions from a Workforce Perspective
Handling port disruptions effectively requires a workforce approach that prioritizes flexibility and cost efficiency. Transitioning to a Cost Per Unit (CPU) model instead of traditional hourly pricing can make a meaningful difference. The CPU model offers a performance-based approach where costs are tied to the units produced or processed rather than hourly labor rates. Here are five strategies on how CPU can help:
- Enhanced Flexibility for Variable Demand
With port disruptions, demand can fluctuate drastically. An hourly workforce model often means inflexible costs, as labor is pre-booked for specific shifts, regardless of the volume of work completed. CPU, however, ties labor costs directly to output, allowing companies to scale up or down according to demand. This flexibility ensures that staffing levels align with real-time needs, making it easier to manage sudden spikes or drops in workflow caused by port disruptions.
- Better Cost Control During Unpredictable Delays
In the face of shipping volatility, businesses need to optimize their costs per unit processed to avoid overspending. Traditional hourly labor charges continue to accrue even when workers are waiting for delayed shipments to arrive. CPU eliminates this inefficiency by aligning labor costs with completed tasks. In the event of a port delay, companies can adjust workforce hours without incurring additional idle time costs, maintaining budget control.
- Improved Workforce Motivation and Performance
The CPU model encourages a performance-driven environment, where employees are incentivized to focus on output rather than hours clocked. This model can improve morale during challenging times, as workers see a direct correlation between their productivity and earnings. During port disruptions, this performance-based approach keeps the workforce motivated to process units quickly and efficiently once goods arrive, helping to minimize further delays.
- Reduced Reliance on Temporary Labor
Port disruptions often require hiring temporary labor to meet shifting demands, which can be costly and difficult to manage. By employing a CPU model, companies can leverage their existing workforce more effectively, relying less on temporary staff. CPU encourages core teams to work at maximum productivity, reducing the need to bring in temporary workers, thereby decreasing labor costs associated with recruiting, onboarding, and training.
- Faster Response to Supply Chain Changes
A CPU model provides businesses with the agility to respond to sudden supply chain changes, such as shifts in port schedules or rerouted shipments. Workforce schedules can be adapted to meet the new delivery timelines without incurring additional costs tied to fixed hourly wages. This agility is crucial in mitigating the impact of port disruptions, as companies can reallocate resources swiftly to keep shipments moving through the supply chain.
CPU as a Long-Term Solution for Volatile Shipping Environments
Transitioning to a CPU-based staffing model is not merely a short-term fix but a strategic shift that prepares companies for a more volatile shipping environment. CPU offers:
- Greater Scalability: CPU’s output-focused cost structure enables businesses to easily scale their workforce up or down as port disruptions require.
- Efficient Resource Utilization: CPU aligns workforce expenses with real productivity, encouraging a more efficient use of resources across logistics operations.
- Incentive for Continuous Improvement: With CPU, employees are incentivized to find faster, more efficient ways of processing units, leading to continuous operational improvements over time.
By investing in a CPU model, companies can build a resilient and agile workforce capable of adapting to today’s unpredictable shipping landscape.
The Final Takeaway
Port disruptions, labor strikes, natural disasters, political instability, and equipment malfunctions will continue to challenge supply chains worldwide. However, by rethinking workforce strategies, logistics managers can mitigate the impact of these challenges. Adopting a Cost Per Unit (CPU) model enables businesses to maintain flexibility, control costs, and keep the workforce motivated—all crucial factors for managing the unpredictable flow of goods through ports.
For operations, logistics, and shipping managers, CPU represents more than just a new pricing model; it’s a strategic advantage. By aligning labor costs with output, companies are better equipped to face the challenges of shipping volatility head-on, ensuring efficient operations and maintaining strong customer relationships, even in the most turbulent times.
About iJility
iJility is a leading provider of workforce optimization solutions, specializing in supply chain operations and on-site management. With a focus on reducing turnover and increasing productivity, iJility delivers customized strategies that align with client-specific goals. Their experienced leadership team integrates data-driven decision-making and innovative solutions to address today’s competitive labor market challenges. Businesses gain access to scalable, dependable workforce solutions designed to optimize operational efficiency and drive measurable results when they partner with iJility.